1、反应精馏的概述
1.1 反应精馏基本原理
反应精馏是在发生化学反应的同时,利用精馏的方法分离反应物与产物,以达到提高产率的目的的过程,在一定程度上将可逆反应转化为了不可逆反应。
1.2 反应精馏的特点
(1)反应段与精馏段的结合,节省了大量的设备费用,减少了设备占地面积。提高了场地利用率。
(2)一部分的反应热可以被利用,节省了能耗,节约了资金。
(3)连续的产物和有机物的分离提高了转化率。
(4)对于二次产物的副反应有抑制作用,可以提高反应转化率。
(5)在反应精馏塔内,各反应物浓度,不同于进料浓度。因此,进料可按反应配比要求,而塔板上造成某种反应物的过量,可是反应后期速度大大提高。同时又达到完全反应,抑或造成主副产物反应速率的差异。从而达到更高的选择性。对比与传统工艺中的某些反应物需要过量从而需要分离回收的情况,能使原料消耗和能量消耗得到大幅度的减缩。
1.3 反应精馏基本工艺流程
以常温常压下典型的液相反应为例A+ B↔C+ D,为例对反应精馏工艺流程作一介绍,并对比其与传统精馏方式的优点。A,B,C,D 四种物质的挥发性大小顺序是,C,A,B,D。其中目标产物为D。传统工艺和反应精馏工艺。
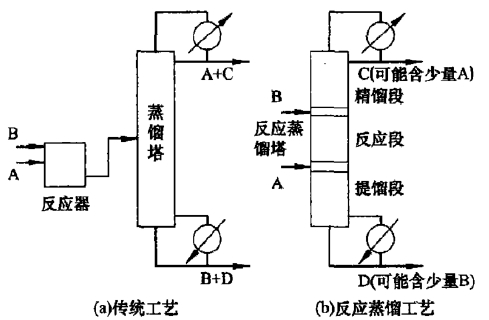
图
1 传统工艺和反应精馏工艺
由图1 中(a)可知,传统的工艺是将A 和B 在反应釜中反应完全后再加入精馏塔中进行分离,由于反应平衡的限制作用,那些进入精馏塔的混合物反应物含量还是较高的。这样分离时可能得不到较纯的产物,而且若不回收未反应的A 和B,将会造成原料的浪费,因此,在精馏塔后一般还设有回收装置,如图1 中(b)所示采用反应精馏技术,原料A 和B 分别从反应段的下方和上方进入反应蒸馏塔,在反应段得到了及时的分离,由于反应和分离相互促进,能得到传统工艺需耗费大量能量,时间才能获得的高转化率和分离效率。反应精馏技术能节省设备投资,减少操作费用,对于可逆放热反应而言,还可以充分利用反应热,从而节省能耗,这些优势使得反应精馏技术成为解决化工高能耗和低原料利用率的有效手段。
1.4 反应精馏的分类
根据投料方式,反应精馏可分为,连续反应精馏和间歇反应精馏,根据催化剂形态不同,反应精馏可以分为均相反应精馏和催化蒸馏,根据反应的快慢,反应精馏分为瞬时反应精馏,快速反应精馏和慢速反应精馏。
2、反应精馏的研究进展
反应精馏的概念于1921 年由Backhaus 首先提出,三十年代到六十年代发展到对固定反应体系的探究,七十年代后进入计算机模拟研究,直到上世纪八十年代才进入到反应精馏基础理论研究的部分。
而最早申请反应精馏专利的是美国的Chevno 公司。美国化学研究特许公司,从1976 年开始研发反应精馏技术,并发表多项专利,其开发的甲基叔丁基醚(MTBE)催化精馏技术于1981 年首先在Charter International Oil 公司的Huston 炼油厂建成了,日产222.6 m3 MTBE 的工业生产装置,实现了这一技术的工业化。
我国的齐鲁石化公司在1988 年从美国引进一套MTBE 的催化精馏装置后,也开发了自己的催化精馏技术,并已在国内外申请了多项专利。该公司开发的催化精馏技术已在上海高桥化工厂实现了工业生产。另外,北京石油化工设计院等单位开发的催化精馏技术已在洛阳炼油厂建成一套年产TBE 2000 t 的生产装置,上海石化研究院也拥有催化精馏生产MTBE的成套技术。1990年世界上催化精馏生产MTBE 的能力已达4324.7 m3 以上。
2003 年,中国石油化工科研院,在研究将催化精馏用于烷基化原料C4 的加氢精制上有了新的突破,采用新的催化体系,RDD-1 NI 系催化剂。该工艺相比传统工艺分离C4-C5 的工艺,流程更为简单,反应条件更容易控制,更有利于使反应向正方向进行,延长催化剂使用寿命。
将液相合成异丙苯工艺与反应精馏结合,以改性的β 沸石FX-01 为催化剂,该技术相比之前的分子筛催化剂技术生产能力要大,工艺更为简单,生产效率有了很大提高。
开发出一种合成乙二醇乙醚的新工艺,采用了新型改性β 沸石合成丙二醇乙醚。新型催化剂比原有的ZSM-5 沸石催化剂的稳定性、选择性和活性都要高,是催化精馏合成丙二醇乙醚的高效催化剂。
利用反应精馏的手段,用EDC作为原料生产TCE,通过实验证明此工艺可行,并且该工艺的最大选择性可大于96 %。
将反应精馏与大通量高效立体式传质塔板相结合,研究出一种生产乙酸乙酯的新工艺方法。该工艺相较传统的反应精馏膜渗透蒸发耦合技术以及反应精馏萃取耦合具有明显的优势,传统膜渗透工艺的膜成本很高,而且由于膜极易被污染,更新成本也很高,而传统萃取耦合工艺单元多,能耗多,流程复杂并不是最优的工艺过程。新工艺成本低,操作简单,污染小,高效的传质塔板显示出了,独特的性能。
利用超重力旋转床催化反应精馏装置,以阳离子交换树脂作为催化的填料。此工艺方法的转化率远远高于新工艺,经过实验证明此方法可行,且可以提高设备的利用率,节省了空间和场地费用。
采用单塔板来定量考察甲缩醛合成反应,在操作过程中,均可自由调节,相较于其他形式,单塔板可逐一的,定量的考察各操作参数对过程的影响,这样的考察不仅能分析单个实验的影响,而且可以分析出传质,传热之间相互的作用因素。所以利用单塔板研究反应精馏是有重要意义的。
3、反应精馏技术的应用与发展前景
3.1 反应精馏的应用
反应精馏适用于反应过程和反应组分的蒸馏分离在同一温度条件下的化学反应。虽然有这一限制条件,但是反应精馏在化工领域的适用范围依然广泛。反应精馏在工业中的应用主要可分为两类:
(1)反应型反应精馏:主要应用于连串反应和可逆反应。在连串反应中,由于精馏的作用使目标产物不断地离开反应区 ,从而抑制副反应的发生,于是反应的选择性得以提高;对于可逆反应,破坏化学平衡,使反应向目标产物进行,反应可趋于完全。现在已被完全工业化的工艺主要有以下4 种:乙酸和乙醇的酯化、甲醛和甲醇在酸性催化剂作用下生成甲缩醛、甲醇和乙酸在一定浓度的H2SO4 作用下生成乙酸甲酯、异丁烯和甲醇在固体强酸性的离子交换树脂催化作用下生成MTBE。
(2)精馏型反应精馏:对于极难分离的共沸物系,反应精馏过程是非常有效的分离手段。
引入反应挟带剂,使其和某一组分发生快速可逆反应,从而增大欲分离组分的相对挥发度而达到分离目的。
目前,该技术在工业中的应用广泛存在于醚化,酯化和水解,烷基化等反应,下面简单介绍。
(1)醚化:醚化反应主要是指甲基叔丁基醚的生产在工业中的应用,甲基叔丁基醚(MTBE)是RD 技术在工业上第一个取得成功的产品,利用反应精馏可以使异丙烯的转化率,大于99 %,比固定床提高3 %~4 %。
(2)酯化和水解反应:乙酸甲酯的合成与水解问题是国内外研究和开发的热门课题。由于乙酸和甲醇的酯化受化学平衡的限制,物系中有多个共沸物,故传统流程十分复杂,需多个反应器共同作用。
(3)烷基化:烷基化产品是一类基本有机化工原料,广泛应用于各行业。反应精馏在烷基化中的应用主要是生产乙苯,异丙苯和合成直链烷基苯。催化精馏技术用于烷基化反应体系,克服了传统工艺的缺点,具有传统烷基化反应技术难以比拟的优点。催化精馏技术在工业过程中的应用表明,该技术不仅大大简化了工艺流程、节约了设备投资和操作费用,而且对环境友好,符合石油化工的发展方向。
3.2 反应精馏的发展前景
反应精馏技术具有广泛的应用前景,加快这项技术的发展,其反应和精馏的过程联系极为紧密,既可以改良工艺,又能提高分离效率。在未来化工的领域反应精馏技术必将有广阔的发展。