工业电除尘器(ESP)种类和结构形式繁多,但是都基于相同的工作原理,主要包括电晕放电、粉尘荷电、荷电粉尘在电场中的迁移运动以及被捕集粉尘的清除。工业电除尘器通常采用负高压直流电晕,即在放电阴极线与接地阳极板之间施加一负直流高压,放电阴极线周围形成大量的正电荷和负电荷,电荷在运动过程中被含尘气流中的粉尘颗粒物捕获,荷有负电荷的粉尘颗粒物在电场的作用下被捕集到接地阳极板,荷有正电荷的粉尘颗粒物则被捕集到放电阴极线。随着电除尘器的运行,阳极板与阴极线上的粉尘颗粒物就会越来越多,形成粉尘层。
阳极板上的粉尘层积累到一定厚度,粉尘颗粒物捕获的电荷很难释放,于是在粉尘层之间形成较大的电势差,当粉尘层之间的电场强度达到击穿电场强度时,便会在粉尘层发生放电即反电晕,反电晕的发生会致使电除尘器电场参数和功率急剧下降,最终降低电除尘器收尘效率,提高电除尘器出口粉尘排放质量浓度。
阴极线“包灰”,即通常所说的阴极线“肥大”,会提高阴极线的起晕电压,而降低电晕电流,导致粉尘颗粒物荷电不充分,进而降低电除尘器收尘效率;如果阴极线“包灰”严重,电晕放电形成的大部分电荷聚集在阴极线表面的粉尘层之内,粉尘层之间电场强度就非常容易达到击穿电场强度,阴极线粉尘层发生反电晕,导致阴极线刚达到起晕放电便发生反电晕,致使电除尘器运行的二次电压和二次电流均很低,此时电除尘器收尘效率显著降低。
电极表面的清灰效果直接影响电除尘器电场运行参数,进而影响电除尘器收尘效率。因此,清灰过程不仅是电除尘器运行的一项基本过程,而且是电除尘器持续高效运行的重要保障。
本文实验选取山西某台有功功率为600 MW的燃煤机组,该机组为超临界参数变压直流炉,一次再热、墙式切圆燃烧、平衡通风、固态排渣、全悬吊结构Π型锅炉,锅炉尾部配备了2 台双室5 电场电除尘器。入炉煤种不仅有当地贫煤,同时掺烧质量分数为75%的泥煤,燃煤灰分高,而且黏性大。该厂对电除尘器的振打系统进行了改造,改造前采用的是顶部电磁振打系统,由于停炉检修发现,电除尘器内部阴极线“包灰”严重,阳极板表面积灰现象明显,清灰效果差,所以改造后采用侧部机械振打系统。本文从振打清灰效果对电除尘器运行参
数的影响这一角度,对振打系统改造前后的振打强度、电除尘器运行参数以及粉尘排放质量浓度进行了跟踪研究。
1、实验条件及参数
1.1 电除尘指数
浙江大学闫克平等经过多年电除尘器基础研究并通过数百台燃煤锅炉电除尘器的跟踪调研与工程应用研究,提出新的电除尘指数方程
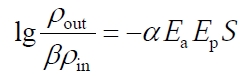
式中: out ρ 为电除尘器出口排放质量浓度,mg/m3;in ρ 为电除尘器入口粉尘质量浓度,mg/m3;
Ea 为电除尘器运行的平均电场强度,0.1 MV/m;
Ep 为电除尘器运行的峰值电场强度,0.1 MV/m;
S 为电除尘器比收尘面积,s/m;α 、β 为无量纲的工况参数。
该方程综合本体大小和电气参数对电除尘器排放的共同影响,其中
Ea
Ep
S 称为电除尘指数,表示单位烟气体积流量在单位收尘面积里获得的电场能量密度,电除尘指数越高,电除尘器排放的限值就越低。电除尘指数方程既包括电除尘器本体参数又包括电除尘器电气参数,能够极为准确地评估电除尘器排放与电除尘指数的关系,在大量燃煤锅炉电除尘器工程改造中得到广泛应用。
1.2 实验概况及参数
表 1、表2、表3、表4 分别为实验期间电厂的锅炉、电除尘器、入炉煤质、粉煤灰成分等基本信息和参数。本文实验包括改造前的顶部电磁振打和改造后的侧部机械振打这2 个部分的内容,为对比2 种振打方式对电除尘器运行效果的影响,实验过程中锅炉负荷、运行工况、燃烧煤种等因素均基本一致,以减少其他因素对实验结果的影响。实验期间,实验机组发电负荷有功功率稳定在600 MW,锅炉长期混烧山西贫煤和质量分数为75%的泥煤,燃煤质量流量约为293 t/h,每台电除尘器处理烟气体积流量约为210×104 m3/h。从表3入炉煤质分析可以看出:燃烧煤种灰分高,水分大。从表4 粉煤灰成分分析可以发现:二氧化硅和三氧化二铝的质量分数之和高达84.7%。浙江大学李晓颖提出的粉煤灰成分与其比电阻的数学关系表明:粉煤灰比电阻与二氧化硅和三氧化二铝的质量分数呈正相关关系,粉煤灰中二氧化硅和三氧化二铝的质量分数越高,粉煤灰比电阻就越大。利用平行圆盘比电阻仪对粉煤灰比电阻进行测试,粉煤灰样取自实验机组电除尘器5 个灰斗,按体积比1:1 进行混合,结果如图1 所示。在实验温度为115 ℃的条件下,锅炉燃烧产生的粉煤灰比电阻接近1013 Ω·cm,属于高比电阻粉尘,被捕集到阳极板上很难释放电荷,粉尘层与阳极板之间形成较强的静电力,因此阳极板的粉尘层很难被振打脱落;同时由于混烧煤种水分大,烟气含湿量高,所以增强了粉尘在阳极板的黏附能力。综上,该厂锅炉燃烧煤种灰分高,比电阻大,黏性大,被捕集到阳极板和黏附在阴极线表面的粉尘层很难被振打脱落。
实验期间,电除尘器电场参数设置如表5 所示。所有电场的二次电压均按照额定值运行,第1、2电场的二次电流按照额定值运行,目的是为了使第1、2 电场以最大功率运行,提高收尘效率。第3、4、5 电场的二次电流分别限制到1000mA、600mA、300mA运行,原因有2个方面:①由于粉尘比电阻大,反电晕强烈,所以降低板电流密度能够有效地控制反电晕;②含尘气流经过第3、4、5 电场,粉尘质量浓度依次降低,粉尘粒径也依次减小,在离子风作用下形成二次扬尘,降低电场二次电流,离子风强度也随之减弱,实现减轻二次扬尘的目的。在整个实验期间,电除尘器电场参数均按照表5 所设置参数来运行。
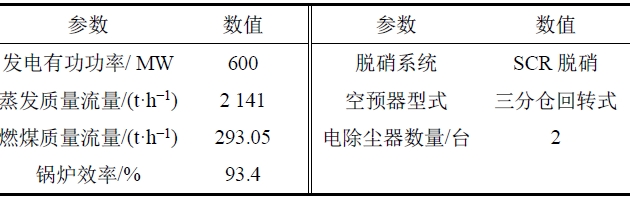
表1 锅炉技术参数
表2 电除尘器技术参数
表3 入炉煤质分析
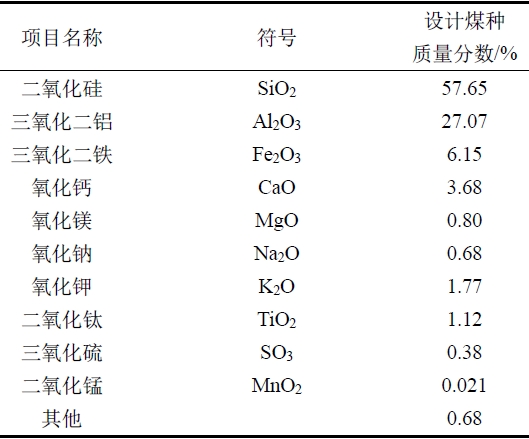
表4 粉煤灰成分分析
图1 实验灰样比电阻
表5 高压电源技术参数
1.3 振打系统
改造前电除尘器采用的是顶部电磁振打系统,振打器位于电除尘器顶部、上顶盖外部,其基本工作过程是:在电磁振打器的线圈通电后,线圈周围产生磁场,振打棒在磁场作用下被吸引提升,提升到设置的振打高度后线圈断电、磁场消失,振打棒在重力作用下自由落体而撞击到振打杆,振打杆位于阴极框架和阳极框架的顶端并与之相连,将撞击产生的振打力自上而下传递到每根阴极线和每块阳极板,从而实现清灰的目的。顶部电磁振打系统结构简单,充分利用电除尘器顶部空间,内部空间占用率小。图2 为顶部电磁振打系统结构示意图。
改造后电除尘器采用的是侧部旋转绕臂机械振打系统,简称侧部机械振打系统,其基本工作过程是:通过振打电机带动振打轴旋转,振打轴与阳极板框架或者阴极线框架相对应的位置布有旋转绕臂,振打锤与旋转绕臂相连,振打轴在旋转过程中,通过旋转绕臂带动振打锤撞击阳极板框架或者阴极线框架的承击砧,从而将撞击产生的振打力按侧向传递到阴极线和阳极板,以完成电极清灰。振打轴、旋转绕臂以及振打锤均安装在电除尘器内底部,相比顶部电磁振打系统,电除尘器内部空间占用率较大。图3 为侧部机械振打系统结构示意图。
①—振打线圈壳体;②—振打棒;③—振打受力点;④—振打杆;⑤—框架悬吊杆;⑥—阴极/阳极框架
图2 顶部电磁振打示意图
①—振打电机;②—电除尘器外壳;③—振打轴支座;④—振打轴;⑤—旋转绕臂;⑥—振打锤;⑦—承击砧/振打受力点;⑧—阴极/阳极框架
图3 侧部机械振打示意图
注:对于顶部电磁振打系统,振打高度为12 cm,振打棒质量为8 kg;对于侧部机械振打系统,振打锤直径为12 cm,振打锤质量为8 kg。
表6 顶部电磁振打和侧部机械振打的参数
1.4 振打加速度
实验期间顶部电磁振打系统和侧部机械振打系统的振打周期和振打参数见表6。对于同一电场的阴极振打和阳极振打,2 种振打系统的振打周期完全一样,表6 中振打周期的时间设置取决于每个电场的收灰量,本文不进行讨论。振打强度与振打棒和振打锤的自身质量呈正相关,振打系统改造前后所采用的振打棒和振打锤的质量也是一样的。对于顶部电磁振打系统而言,振打棒提升高度即振打高度与振打强度呈正相关,但由于顶部电磁振打系统对绝缘瓷套有严重损害作用,因此实验过程中,顶部电磁振打系统的振打高度最大为12 cm。
由于电除尘器的阳极板和阴极线数量极多,所以不能逐一进行振打加速度的测试;对于相同的振打方式,阴极框架和阳极框架的振打特点相同,而且阳极板容易布置振打传感器,因此,实验只选取了同一个电场的同一个阳极板框架进行不同振打方式的振打加速度测试。图4 为振打加速度测点示意图,实验阳极板框架中含有6 块C480 阳极板,从左至右依次编号1—6,阳极板高度为15 m,自下而上每隔1 m 高度设个测点,依次编号1—14,总计84 个测点。
表 7 和表8 分别是顶部电磁振打和侧部机械振打的振打加速度测试结果。顶部电磁振打加速度分布特点是阳极板自上而下依次降低,对于同一个阳极框架中的各个阳极板相同位置处的振打加速度分布一致;侧部机械振打加速度分布特点是阳极板自下而上依次降低,对于同一个阳极框架中靠近振打承击砧处的阳极板振打加速度最大,如表8 所示,阳极板6 的振打加速度最大。实验测试结果表明:顶部电磁振打加速度最大值为162
g,加速度分布均方根最大为 0.64;侧部机械振打加速度最大值为458
g,加速度分布均方根最大为0.44;侧部机械振打加速度平均值约为顶部电磁振打的3 倍。综上,在相同振打周期、相同振打棒质量和振打锤质量的条件下,侧部机械振打产生的振打加速度约为顶部电磁振打的3 倍,而且振打加速度分布较为均匀。
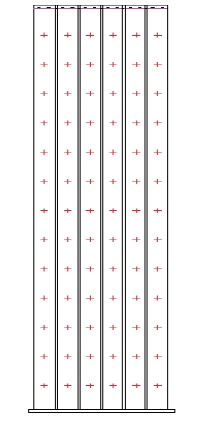
图4 振打加速度测点示意图
表7 顶部电磁振打加速度测试结果
注:柱状图表示二次电压;折线图表示二次电流。
图 5 2 种振打形式电除尘器运行参数
表8 侧部机械振打加速度测试结果
2、电除尘器运行参数对比分析
图 5 为采用顶部电磁振打和侧部机械振打条件下电除尘器运行的电场参数。
对于该电厂燃煤煤种而言,从图5 可以看出:采用顶部电磁振打系统,第1、2 电场的电气运行参数均较低,伴有频繁的闪络;第1 电场的二次电流为249 mA,二次电压为42 kV,闪络频次为50~60次/min;第2 电场的二次电流为554 mA,二次电压为51 kV,闪络频次约为20 次/min。造成电除尘器运行参数较低的原因是振打力度不够,阴极线和阳极板的粉尘打不下来,阴极线包灰严重,阳极板粉尘层太厚,分别在阴极线和阳极板的粉尘层间发生反电晕。从第1 电场的电气运行参数可以看出:在阴极线起晕阶段或者较低电晕电流的情况下,电场便发生闪络,表明阴极线包灰严重,电晕形成的电荷积累在阴极线周围的粉尘层表面,发生阴极线粉尘层放电,这种情况下电晕电荷很难被粉尘捕获,二次电压和二次电流参数非常低,因而收尘效率大幅度降低;由于第1 电场收尘效率差,第2 电场的粉尘质量浓度仍然很高,但是与第1 电场有明显的区别,第2 电场主要是阳极板的粉尘层在放电,在这种情况下,电晕电荷可以被粉尘捕获,但是由于闪络存在,迫使已被捕集到阳极板的粉尘再次进入电场中去,降低电除尘器收尘效率。经过第1、2电场后,粉尘质量浓度大幅度降低,捕集到阳极板的粉尘灰量减少,顶部电磁振打清灰效果满足需要,因此第3、4、5 电场运行正常,无闪络现象,运行参数基本达到设定值。
顶部电磁振打更换侧部机械振打后,电场闪络频次有效控制,第1、2 电场的二次电流有显著的提高,第1 电场的二次电流由249 mA 提高至669 mA,二次电压由42 kV 提高至59 kV,闪络频次降低至20 次/min;第2 电场的二次电流由554 mA 提高至1197 mA,二次电压基本保持不变,闪络频次降低至5 次/min。第1、2 电场的运行参数表明更换侧部机械振打后,阴极线和阳极板表面清洁,积累的粉尘层被振打下来,有效控制了反电晕现象。第1 电场无论二次电压还是二次电流都有大幅度提升,说明阴极线包灰情况基本消除,阴极线放电良好,但是由于第1 电场粉尘质量浓度高,电晕放电产生的电荷被粉尘颗粒捕获,所以二次电流只有669 mA,二次电压高达59 kV,远高于第2 电场,这是由于ZH2013T 系列三相高效电源控制系统的优点决定的,该电源控制系统为二次电流自动跟踪系统,当二次电流达不到设计值时,控制系统便会自动提升电压,并自动判断火花电压。粉尘经过第1 电场质量浓度降低,第2 电场基本消除闪络现象,二次电流接近额定值运行,二次电压基本不变,也说明顶部电磁振打清灰效果差,第2 电场阳极板的粉尘层发生反电晕现象。第3、4、5 电场由于粉尘质量浓度的降低,二次电流基本可以按照设定值运行,二次电压较之顶部电磁振打时,有1~2 kV 下降幅度。
第 1、2 电场粉尘质量浓度高,运行二次电流低,便自动提升二次电压,提高电除尘器收尘效率;第3、4、5 电场粉尘质量浓度低,采用限流模式运行,降低离子风的二次扬尘效应,这都取决于ZH2013T 系列三相高效电源先进的自动跟踪控制系统。图6 对比了这2 种振打形式下,电除尘器一个室的每个电场输入功率,更换为侧部机械振打系统后,第1、2 电场输入容量明显提高,第3、4、5 电场稍微降低,电除尘器每个室电源总输入容量由 131 kVA 提高至190 kVA。
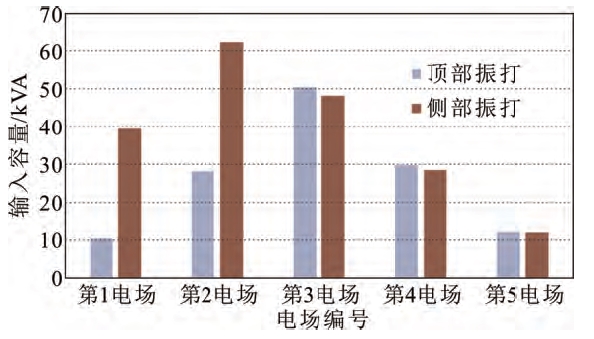
图 6 2 种振打形式电除尘器输入容量
3、电除尘器排放对比分析
图 7 和图8 分别为电除尘器出口粉层数密度分布和质量浓度粒径分布,对比了顶部电磁振打和侧部机械振打电除尘器出口排放特点。在这2 种振打形式下,电除尘器出口粉尘粒径分布有明显变化,更换为侧部机械振打系统后,对于粒径介于0.1~10 μm 之间的粉尘排放质量浓度明显降低,对于粒径小于0.1 μm 和粒径大于10 μm 的粉尘,排放质量浓度则变化不大。这是因为对于0.1~10 μm 粒径范围内的粉尘,粒径小,荷电困难,对其捕集需要高电压和大电流共同作用;对于粒径大于10 μm 的粉尘,粒径大,荷电能力强,所受到的电场力较大,所以在低电压和小电流的条件下仍有较高的收尘效率;而对于粒径小于0.1 μm 的粉尘,质量非常小,非常容易受到振打影响而形成二次扬尘,所以更换为侧部机械振打条件下的电除尘器排放数密度呈增加趋势。
此外,从图8 电除尘器出口粉尘质量浓度粒径分布可以看出:无论是顶部电磁振打还是侧部机械振打,在0.5 μm 粒径附近都存在电除尘器出口排放的凹点。在以往荷电量与收尘效率关系研究文献中介绍,0.5 μm 粒径附近颗粒物的荷电方式是电场荷电和扩散荷电共同存在,在相同电压和电流条件下,其荷电量低,该粒径段颗粒物的排放呈现凸点。本文实验结果与传统研究结果不一致的原因是:由于该粒径段颗粒物荷电量低,于是非常容易受气流场的影响,而本文实验中第3、4、5 电场的二次电流都是限流优化模式运行,二次电流降低,形成的离子风弱,对0.5 μm 粒径段的颗粒物二次扬尘作用小,所以排放质量浓度较低。
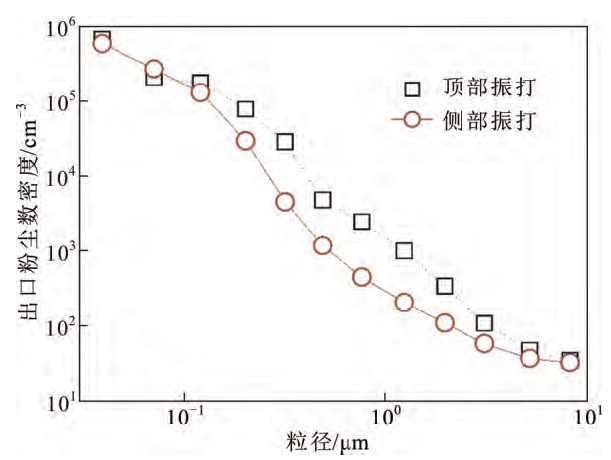
图7 电除尘器出口粉尘数密度粒径分布
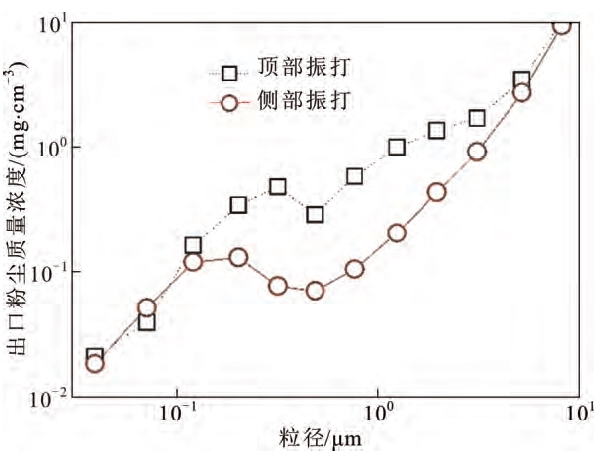
图8 电除尘器出口粉尘质量浓度粒径分布
图9 电除尘器出口PM10 和PM2.5 排放质量浓度
图 9 对比了顶部电磁振打系统和侧部机械振打系统电除尘器出口PM10 和PM2.5 排放质量浓度。更换为侧部机械振打系统后,PM10 排放质量浓度由19.33 mg/m3 降低至14.14 mg/m3,降低比例为26.85%;PM2.5 排放质量浓度由4.23 mg/m3 降低至1.20 mg/m3,降低比例为71.53%。
更换为侧部机械振打系统后,第1、2 电场对PM2.5 收尘效率的提高十分显著,这主要取决于PM2.5 在电场中的动力行为特征。由于PM2.5 粒径小,荷电量低,所以如果要提高PM2.5 的收尘效率,就非常依赖高电压和大电流;同时由于粒径小,质量轻,所以又非常容易受到振打以及离子风影响形成二次扬尘。更换为侧部机械振打系统后,大幅度提高了第1、2 电场运行的二次电压和二次电流,保证了对PM2.5 的收尘效率高;同时第3、4、5 电场采取限流模式运行,降低了离子风对PM2.5 的二次扬尘效应,这是更换侧部机械振打系统后PM2.5 排放质量浓度显著降低的主要原因。
4、结论
1)在相同振打棒质量和振打锤质量的条件下,侧部机械振打产生的振打加速度平均值约为顶部电磁振打的3 倍,采用侧部机械振打同一块阳极板的振打加速度分布较为均匀。
2)对于燃煤灰分大、比电阻高、常规有功功率为600 MW 的燃煤机组电除尘器,通过更换顶部电磁振打系统为侧部机械振打系统,电除尘器每个通道的电源输入容量可由131 kVA 提高至190kVA;PM10 排放质量浓度由19.33 mg/m3 降低至14.14 mg/m3,降低比例为26.85%;PM2.5 排放质量浓度由 4.23 mg/m3 降低至1.20 mg/m3,降低比例为71.53%。