本文围绕计算机技术设计与优化机械结构现状,总结与归纳机械机构的设计与优化方法,从中得出计算机技术的机械机构优化理念。以便能够用更为科学的理论作为指导,实现高品质的机械机构优化设计。根据现如今国内外的机械产品优化设计方式特点,可以将其分为三类,分别为结构模块、系统模块、产品特征描述。
1 结构模块的优化设计
这种优化方式,即结合产品规划不同角度提出不同优化方法。也就是说,结构模块优化是按照产品规划出发,将规划分解成单独的任务,从源头处解决优化问题,在减少产品问题的基础上,实现高效的工作效率。用这样的方式,能够在保障优化设计质量的同时,提高优化设计的效率。机械机构设计应尊重产品的原设计和规划,站在细节方面进行优化。
结合Feldman 理念,在优化产品结构时,需要涉及到产品四个任务功能,包括功能原件、功能组件、功能组成、产品。优秀高品质的模块结构能够实现配合与连接并行,有标准化接口,能够在灵便化、通用化、经济化、层次化、系列化、集成化的过程中,产生相容性、互换性、相关性特征。在此基础上,进行机械结构的设计与优化时,还要结合CAD 制图技术与软件设计,实现优化过程中的变形设计与组合设计。根据分级原理,将机械机构结构模块按照大小分级,将其分为原件、组件、部件、产品四个等级。
在制定机械机构的优化设计方案用功能模块区分功能区域是非常常见的方法。功能分解能够将基础粒化,使机械机构与功能一一对应。这样机械机构模块便能够实现映射效果,是提高机械机构优化顺利进行的重要前提。
2 系统模块的优化设计
系统优化指的是,设计人员先将机械机构视作一个整体,将优化流程看作是完整的结构。将每一个优化元素视作单独的部件,明确这些单独部件存在密切联系的关系。这样的层次化设计,能够实现设计元素既是单独的个体,又是共同的整体,能够达成整体优化的目的。目前来看,机械机构优化系统模式一般是按照德国VDI2221 设计方式。当然也有一些机构优化系统采用的是我国自主研发的系统设想。
根据用户需求进行机械结构设计,质量功能分部位首先根据用户需求明确机械结构基本功能和特征,之后根据机械结构的功能特征确定各个零部件的特征。将零部件特征作为核心,在讨论和实验的过程中明确零件工艺特征。最后按照工艺特征分析,得出系统优化作业特征,决定最后的系统优化方法。
系统优化与设计建立在将产品视作整体系统,通过不同区域和不同特征的规划与明确,实现产品的整体性设计,最终得出产品成品的设计结果。代表性设计方法包括键合图法、举证设计法、构思设计法、图形建模法、设计元素法等。每一种方法都需要结合系统完成优化设计方法与方案的制定。
3 产品特征的优化设计
在优化设计机械系统的结构时,需要根据产品发展特点,进行相对应的优化设计。在此过程中最重要的技术就是计算机辅助,计算机辅助贯穿于机械产品优化设计的始终,能够帮助设计人员提高优化设计效果和自动化水平,完成机械机构优化的管理、协调、表达。总结来说,现如今产品特征优化主要包括如下方法。首先是实例法。实例法通过框架结构完成概念实体、工程实例描述。在推理的过程中获取候选资源,并将候选资源匹配进入到优化防范与匹配设计。其次为编码法,这种方式结合运动转换,实现机构整理与分离。通过知识库搜集与整理方式,完成机械结构优化设计,确定优化设计的方案。最后是混合性表达,这种方式将网络系统、框架、过程、规则进行整合,实现高质量的产品特征设计。CAD 软件中, 常用NEXPERTOBJECT完成优化方案制定。在结束目录优化与否设计以后,实现机构组、功能模块、功能分解的组织优化,为优化提供辅助工效。上述方法全部需要在实际应用中,根据产品自身特点进行选择。
4 机械结构具体优化方法
现如今机械解耦股优化主要存在两个问题,包括设计参数、设计规则两个因素,这些问题是导致设计好坏的关键。
4.1 结构参数优化
机械结构优化涉及到数千个设计变量,与数百个设计函数。由于包含大量的函数和设计变量,所以在设计程序时需要面对很大困难。针对这一问题,在设计时需要建立参数信息模型,这样才能够在优化时,有参数借鉴,提高设计优化效果。详见图1。
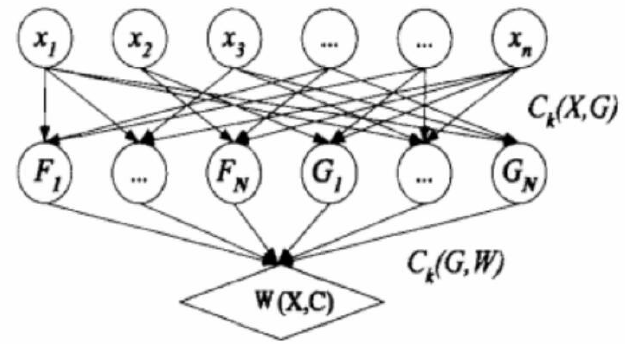
图1 参数信息优化模型
从图1 可以得知,在优化参数时,需要先行提出x1、x2…xn 作为优化设计的基本参数,是数据输入;而F1、F2…FN则是目标函数;G1、G2…GN 是约束函数,是数据处理与数据分析阶段。W(X,C)是修正函数,是数据输出阶段。通过输入阶段的分析与处理,得出的数据传递系数即Gk ( X,G)(k=1,2,3…N)是设计变量转化为约束函数与目标函数的过程。通过数据处理与分析,得出数据修正因素Ck ( G,W)(k=1,2,3…N),通过对修正因素分析得出约束函数与目标函数的最终结果修正函数W(W,C)。结合数据模型分析,得知各个参数关系。这一模型特点非常显著,再结合麦克劳林算法与QFD 理论,能够找出机械设计参数最小属性集。
4.2 规则提取
通过提取优化规则,才能够改变模型设计参数,得出有效的优化实例。在进行元方针计算时,将结果计入数据库,通过管理系统将数据离散,采集数据有限元。用粗糙集理论分析有限元,挖掘数据提取数据优化规则。本次选择门式小车架优化实例分析,将粗糙集理论作为优化技术,通过提出参数模型参数,挖掘小车结构参数规则。根据大量有限元结果与实践经验,认为有5 个参数与几何条件和小车架构特性有关。包括梁1 厚度,简称L1T,与梁2 厚度,简称L2T,梁5 受转矩,简称RT1,小车钢丝绳拉力,简称RT2。梁2 与梁5 距离,简称DIS。梁7 宽度,简称为L7W。详见图2。
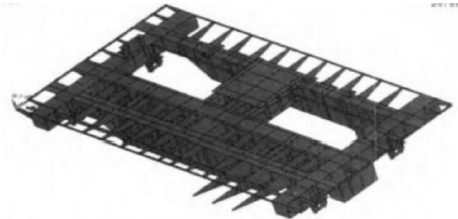
图2 门式小车架有限元模型
以上六个条件是本次优化小车的基础条件,是分析小车架结构能够优化的先决前提。参数合理与否是小车优化的决策属性,应结合不同组件应力状况确定。组件选择与组件应力关系,需要通过样机受力情况比较确定。通过行列计算法与增类减类法离散方式,计算最终离散决策表。
从提取的规则可以判断如果L1T 等于1,RT1 等于2,DIS等于1。那么最大应力为3。即如果梁1 厚度大,且梁5 受转矩大,则梁1 与梁7 底部会出现较大受挤压力。此时应力值将会超过材料许可应力值,影响小车架结构的稳定性,所以应避免这种情况发生。如果RT2 等于2,RT1 等于1 或2,则表明最大应力为1.即如果梁1 厚度薄,梁5 钢丝绳拉力大,则梁5 底板应力最大。如果DIS 等于2,RT2 等于1,那么最大应力为2. 即如果梁2 与梁5 存在较大距离,梁2 厚度搅拌,则梁1 与梁2 底部应力最大。通过上述方式能够提取大量有用的优化规则,将这些规则代入智能分析系统,可以实现机械机构的有效设计和优化。
5 结语
机械机构设计与优化必然会在发展的过程中,受到先进技术影响。现如今我国也将机械产品的机构优化,朝向计算机结合方向前进。如今机械机构的创新设计与优化方法在国内外均已经获得了广泛的关注,并取得了一些成效。我国设计学者也意识到了CAD 制图的应用价值,广泛的使用CAD 制图实现机械机构的设计与优化。可以说未来的机械行业发展,是一定离不开机械结构优化的。