当前,我们正经历一场新的技术革命,这场技术革命以信息技术为中心,以极大地提高工作效率为目标。
在这种新技术革命的影响和冲击下,使传统的机械工业焕发了青春,同时也使工程机械行业发生了深刻变化,信息技术的广泛采用使工程机械的功能增多,各项性能大幅提高,性能价格比大为改善。
信息技术包括三大支柱,即:测量与控制技术、计算机技术、通信技术。近些年来这些技术取得飞速发展,并在工程机械传动技术方面不断得到应用。例如,在国外,日本小松公司推出了20t级PC200-8型混合动力挖掘机,采用并联式混合动力系统,比传统动力的挖掘机可节省燃料20%以上,同时NOx、CO2排量进一步减少。
卡特彼勒推出了966KXE中型轮式装载机,采用了带变速控制系统的电控静液压传动装置,燃油效率提高25%;在国内,西筑WT750型摊铺机采用德国力士乐微控制器系统MC6,可实现恒速控制功能,采用双泵、双马达左右独立驱动的液压调速闭式回路,转向圆滑,低速行走平稳。信息化在工程机械传动技术方面,国际国内成功应用的例子还有很多,可以说不胜枚举。
目前信息化技术还处于强劲的发展之中,所以工程机械信息化的进程还远没有结束,在未来,综合信息化还会对工程机械传动技术产生巨大的影响,总结其发展趋势归结为以下4个方面。
1、由流体、机械处理动力流信息逐渐走向由微电子技术处理动力流信息
早期的工程机械与现代意义上的信息技术关联不大,其动力流信息的处理主要靠机械、流体本身完成。
1.1液压技术方面
早期的开式液压系统主要采用滑阀来控制动力流走向,滑阀是典型的用机械处理动力流信息的部件。后来为了实现对传动系统精确的力、位移控制,出现了伺服阀与比例阀。伺服阀因对油液的过滤精度要求较高,在工程机械传动上的应用较少,相比之下比例阀的应用比较广泛,图1是使用比例阀对油缸位移进行伺服控制的原理图。
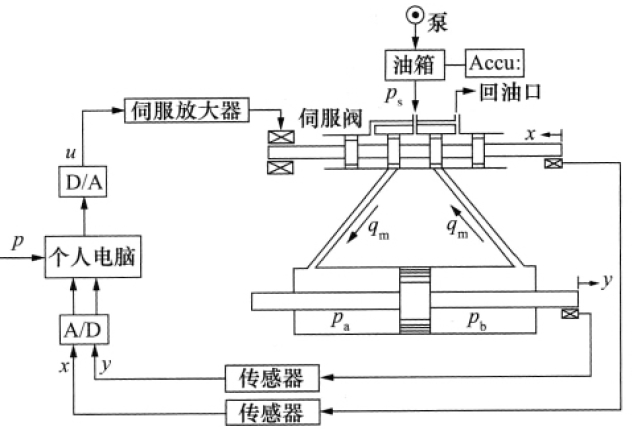
图1使用比例阀对油缸进行位移伺服控制原理图
伺服阀与比例阀对动力流的控制是在机械、流体控制的基础上增加了微电子控制,且微电子控制部分更多地决定了控制性能,代表了从机械、流体控制为主走向以微电子控制为主时代的到来。
但是在伺服阀与比例阀对动力流的控制中,机械的控制仍然占有相当的成分,因为它们没有摆脱滑阀控制的物理基础。图2a显示出了图1中三位四通阀控制口的特性与图2b中惠斯顿电桥各边的特性对应关系,从中可以看出滑阀的控制特性完全可以用电学上的桥路控制特性来代替。
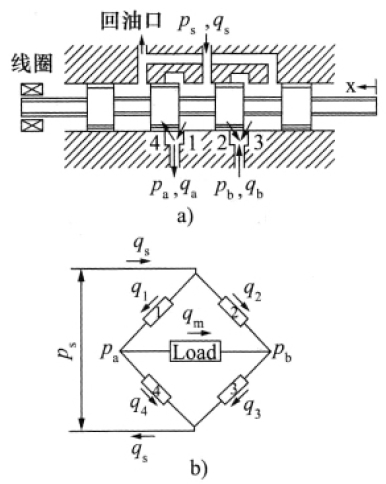
图2三位四通阀与惠斯顿桥路的关系
图3是利用桥路的基本原理使用电磁阀或高速开关阀来构成的与图2a具有相同驱动功能的驱动系统。图中的系统若频响要求低时可使用普通电磁阀,若频响要求较高时,可使用高速开关阀。
图3所示的系统中机械与液压对动力流信息的处理功能进一步弱化,其功能更多地被信息技术所取代,与原系统相比在控制方法上具有了更多的灵活性。
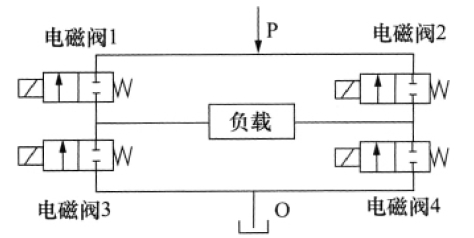
图3利用桥路原理构成的负载驱动油路
随着工程施工机械向大型化方向发展,大输出的液压元件被用于工程机械上,为了操作省力,液压控制系统随之采用了先导控制液压系统,先导控制起到了动力放大器的作用,是处理动力流信息的一种方式。
随着液压技术的进步,我们习惯了越来越多地采用了液压本身来处理动力流信息。
为了提高液压系统的控制功能,采用了复杂的多路阀。多路阀是以两个以上换向阀为主体,集单向阀、过载阀、补油阀、制动阀及压力补偿器等于一体的集成阀。如图4所示为Rexroth-LUDV多路阀,即负载独立流量分配阀。可实现单泵—多执行器系统的复合动作。

1.行程限制2.工作口过载补油阀3.单向阀4.LUDV压力补偿器5.单向节流器6.主阀芯7.进油测量阀口8、9.回油阀10.进油槽
图4Rexroth-LUDV多路阀结构图
为了实现节能、降噪、提高工作效率及工作平稳性控制方面的功能,液压泵采用复杂的油路将恒功率、全功率、交叉功率、压力切断、负载敏感、正流量、负流量控制回路等集于液压泵中。
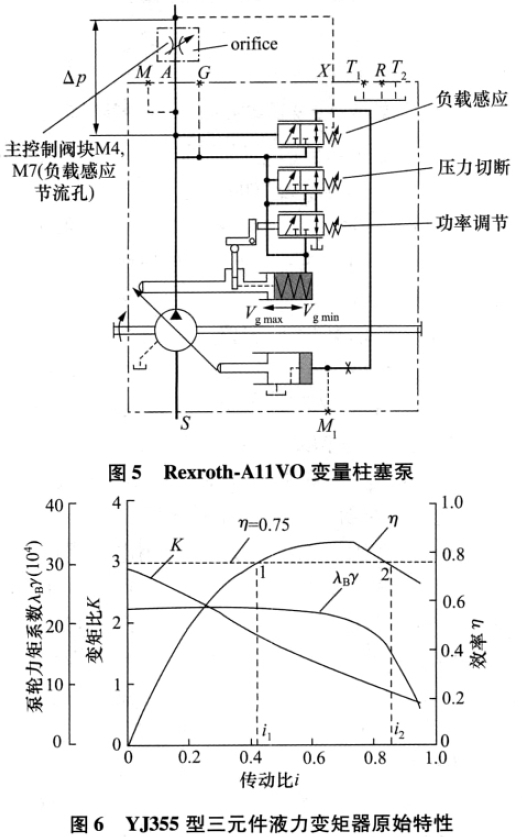
图5所示为Rexroth-A11VO变量柱塞泵,它具有恒功率、压力切断、负载敏感控制,可应用于混凝土泵车、铲运机械、混凝土机械、路面机械、压实机械及起重机械等工程机械领域。
无论是前面所说的多路阀、还是多功能泵,其制造工艺复杂、成本高,使用液压与机械承载了较多的动力流信息处理功能,这些功能可否用现代信息技术来解决呢?答案是肯定的,并且是一种发展趋势。
1.2液力技术方面
液力变矩器是人类在流体传动领域最伟大的发明之一,它巧妙利用了泵轮与涡轮之间的相对转速不同,使流体动压力冲向叶片角度不同的原理,实现了自动变矩的功能。早期的液力变矩器为简单的三元件液力变矩器,其高效区范围(传动效率大于75%的区域)较窄,图6是YJ355型三元件液力变矩器原始特性。从中可以看出,当传动系统提供的力矩不足以克服过大的负载时,变矩器涡转转速就会下降,在泵轮转速(同发动机转速)相对不变的情况下,转速比i降低,变矩比增大。反之当传动系统提供的力矩大于负载时,则变化趋势正好相反。这就是变矩器的变矩功能,也是使用液力技术处理动力流信息的典型例证。
液力传动有个比较大的弱点就是其传动效率较低,尤其是当遇到较重的负载需要传动系统输出较大功率时,液力变矩器的传动效率反而大幅度下降甚至降低为零。它使作业效率降低造成了能源的浪费。浪费的能源转化为热量使油温升高导致机器工作环境恶化故障率上升。
针对这一情况,近年来国内外的研究者与技术人员主要通过设计双泵轮、双导轮、双涡轮和反转导轮机构等措施来提高变矩器的效率和高效区范围,这些措施取得了一定成效,但并没有从根本上解决重载下传动效率下降的问题,这一点从图7所示的双涡轮液力变矩器原始特性曲线即可看出。
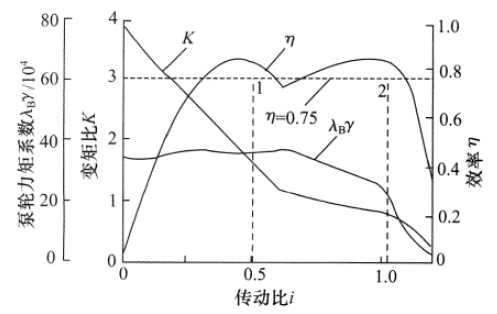
图7双涡轮液力变矩器结构简图及原始特性曲线
这些复杂变矩器的改进过程同时也可以看成是对其动力流信息处理技术改进的过程。
从以上可以看出,在工程机械中广泛采用的液力传动技术不只是动力执行部件,而且还承载了更多地动力流信息传感与处理的功能。但是,用流体配合机械来处理动力流信息与使用现代微电子技术来处理信息相比,总体上讲后者应该更加简便,快捷与节能。除此之外,微电子技术还可以通过软件来处理一些信息,这是机械、流体处理信息所不能相比。
从图6与图7的变矩比特性曲线(K-i曲线)可以看出,它与调速电机的调速特性相近,所以近年来在几种混合动力装载机的传动系统中,使用电机辅助传动的方式取代了液力变矩器,事实上是运用微电子技术处理动力流信息代替了用液力技术处理动力流信息,并且运用电传动代替了液力传动,下面介绍两个例子。
川崎65ZHybrid混合动力装载机,采用由行星齿轮和电机辅助驱动的方式取消了液力变矩器,如图8所示。当传动系统遇到重载,发动机所提供的力矩不足以驱动装载机行走时,电机通过行星排辅助驱动主传动系,起到与变矩器相同的功能。除此之外,该系统还可以将装载机刹车时的能量收集起来以便以后重复利用。该型混合动力装载机比同级别普通装载机相比可节省燃油35%以上。
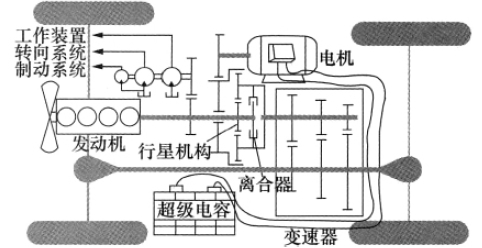
图8川崎65ZHybrid混合动力装载机系统原理图
约翰迪尔644KHybrid混合动力装载机,用柴油机驱动发电机和工作泵,由电力驱动变速箱,同样是利用了信息技术来处理主传动系统的动力流信息,并利用了调速电机的调速特性。如图9所示。发动机运行在恒定的1800r/min这一燃烧效率最高的转速时,使传动动力可以随时响应,同时也保证了液压系统可以提供最大的动力输出,发动机总是在低油耗区工作,燃烧效率高、噪声低、对环境的污染也较小,在不牺牲性能的情况下,644KHybrid预期燃料消耗可减少约25%。
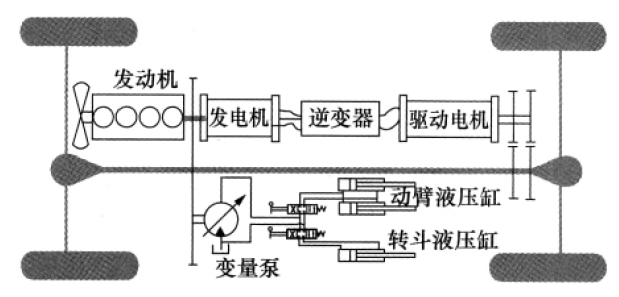
图9约翰迪尔644KHybrid混合动力装载机系统原理图
综上所术,工程机械传动系统中原来由机械、流体处理动力流信息的技术逐渐被微电子技术处理所代替,随着信息技术的飞速发展,未来这样的发展趋势还会继续下去。
2、由复杂的多路阀控制的流体动力系统逐渐走向由总线和分立电控元件控制的动力系统
近年来总线技术的发展,使信息化技术如虎添翼,从早期的RS232/485总线到目前广泛应用的CAN总线,其可靠性、抗干扰能力有了很大程度的提高,线束的根数已经减少到了构成回路的最少数量(2根)。在总线技术发展的推动下,工程机械原来使用的一些液压操纵机构已经变为总线驱动的“线控”操纵机构。
为了便于数字驱动,使液压系统更便捷地实现信息化,出现了数字液压执行元件,其典型代表为高速开关阀与比例阀。高速开关阀使用PWM(PulseWidthModulation)对流量或压力进行控制,响应时间一般为毫秒级,对普通液压执行元件如缸与马达的控制能够满足工程机械工作响应的需要,抗污染能力强,成本也比较低。
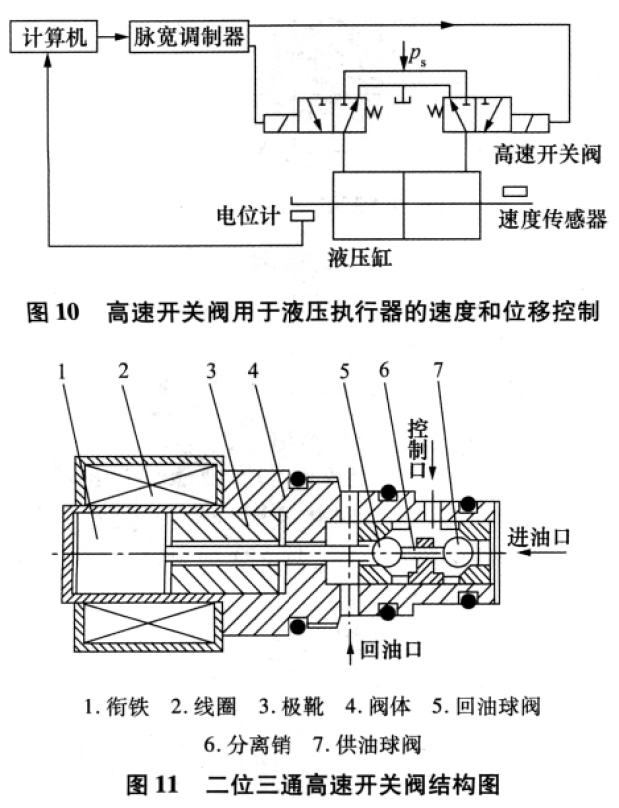
用高速开关阀可以构成一个数字伺服控制系统,以实现如挖掘机、起重机等工程机械、运输机械的数字控制和远距离控制。如图10所示,执行机构活塞杆位移控制可通过计算机根据PWM方式将相应的控制信号分别送到两个二位三通高速开关阀(结构图如图11),并由这两个高速开关阀分别控制进人执行机构两腔的流量,从而控制活塞杆的速度和位移。
高速开关阀与逻辑阀配合可进行大流量控制,高速开关阀控制逻辑锥阀,还可以进行较大流量的比例控制。当采用PWM控制改变高速开关阀的变调频率时,锥阀的开启率也将相应变化,流量将基本上与高速开关阀的变调率成正比。
另一个易于进行数字控制的阀就是比例阀。比例阀的性能介于伺服阀与高速开关阀之间,可以对阀流量或压力进行连续控制,而抗污染能力与滑阀相同,因此比例阀在工程机械中得到了广泛应用。因为可用PWM进行控制,所以便于通过CAN总线传输控制信号。比例阀与PWM及CAN总线的结合是工程机械信息化技术的巨大进步。
MOOG公司的D638系列直动式数字伺服比例阀,能够实现CAN总线通讯,每个阀的操作相对独立,不仅可通过计算机进行控制,也可以使用PLC对阀参数进行调整,在阀工作时还能对其进行实时调整。博世力士乐公司的IAC-R高频响比例阀,配置CANopen总线,上位机通过现场总线与数字控制器进行实时通讯,控制器中的数字控制系统承担阀控制器的职能。这些新型比例阀都已得到应用,小松、卡特彼勒多个型号挖掘机配备了上述产品,极大地改善了性能。
3、电传动的应用逐步增多
工程机械广泛采用复合传动,早期的工程机械主要使用机械与流体传动,如大家所熟知的变速箱是机械传动,液力变矩器液力传动,动臂油缸的驱动是液压传动。电传动只有在特大型矿山装备中有少量的使用。相对于机械与流体传动,用微电子技术来控制电驱动要来得更加便捷,近年来随着信息化的到来,以及电机技术和电力电子技术的巨大进步,电驱动技术在工程机械传动中的应用越来越广泛。
日本小松公司生产的PC200-8型混合动力挖掘机,其机体回转的驱动就由原来的液压驱动改为电驱动。在改为电驱动以后,不仅回转的控制更易于实现,而且便于回转部件动能的快速回收与重复利用。回转部分减速时,回转马达将减速制动时产生的能量转化为电能回收,并将其储存在蓄电器中。在回转加速时,再将储存的能量加以利用,或者通过电动/发电机将其用于作业时发动机加速的辅助能量。图12是小松公司PC200-8混合动力系统结构示意图。
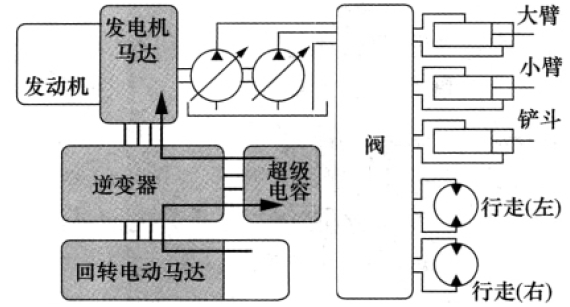
图12小松PC200-8混合动力系统结构示意图
在第一节中提到的川崎65ZHybrid混合动力装载机与约翰迪尔644KHybrid混合动力装载机,其主传动是由电驱动取代了液力传动,是复合传动系统中电传动的应用增多趋势在液力传动领域的具体体现。
4、动力源的输出向恒功率输出方向发展
工程机械总体上是间歇工作的机械,如装载机的铲装作业,动臂、铲斗的运动都是间歇式的。为了减少恒压系统溢流损失,多数工程机械的工作装置的控制滑阀组中位多使用卸荷的结构,如图13所示。但工程机械多用柴油机驱动,因工作装置间歇工作引起的载荷剧烈波动会使发动机燃烧特性变差,不但经济性变差,而且会使碳排量增加,污染环境。
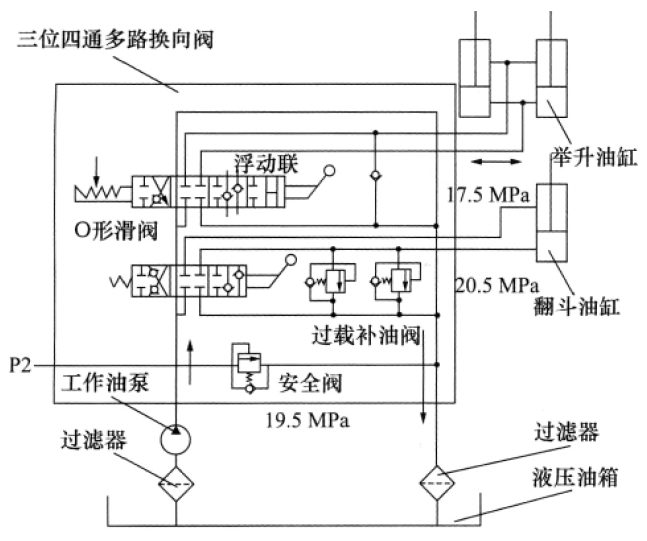
图13ZL50型装载机用换向阀
近年来汽车工业使用混合动力技术,在稳定发动机到低油耗工况、以及节能与减排方面取得了突出的成绩。与汽车相比工程机械工作时的载荷波动更大,稳定发动机到低油耗工况并实现恒功率输出也具有更大的挑战性,不过使用混合动力技术实现节能的潜力也更大。因此近年来出现了多种类型混合动力的工程机械,最主要的有液压混合动力工程机械和电混合动力工程机械两种。
首先介绍液压混合动力工程机械,图14为一种液压混合动力装载机原理方案,其主传动系统采用液压混合动力技术,通过二次调节技术回收制动能,降低燃油消耗和尾气排放,并提高整机动力性能。根据徐工集团推出的ZL50G液压混合动力装载机提供的报告,整机节能达25%,制动回收率达75%。
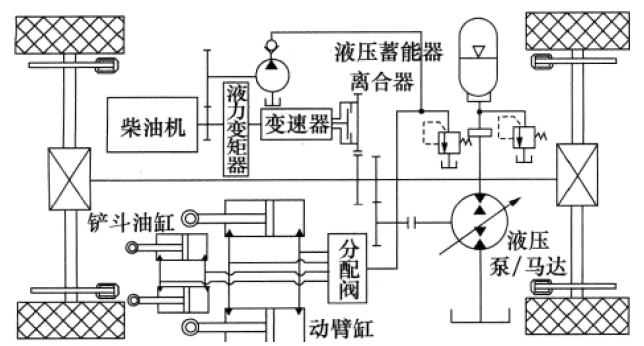
图14徐工集团ZL50G液压混合动力装载机及原理图
下面介绍电混合动力工程机械,在电混合动力装载机方面,2008年推出了世界首台混合动力轮式装载机———沃尔沃L220FHybrid,如图15所示,该机通过在发动机输出轴上安装ISG电动/发电机,构成了并联式混合动力电驱动系统,据报道可节省燃料10%。
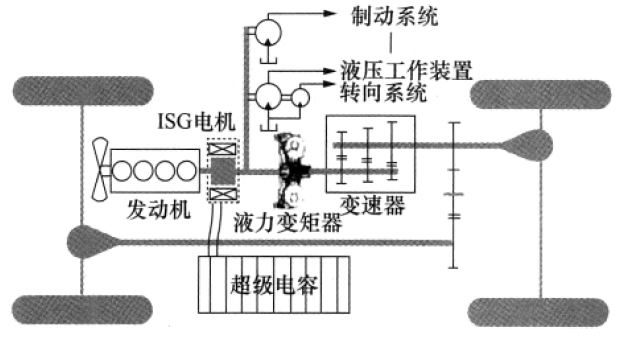
图15沃尔沃L220FHybrid轮式装载机
另外,前面第一节介绍过的川崎65ZHybrid装载机与约翰迪尔644KHybrid装载机,分别是并联与串联电混合动力装载机。
在电混合动力挖掘机方面,相关文献报道较多,这里只介绍几种。
图16为日立建机电混合动力液压挖掘机的结构示意图。该机采用了并联式电混合动力系统,回转部分与行走部分分开控制,两者之间通过两个整流逆变器进行电连接。
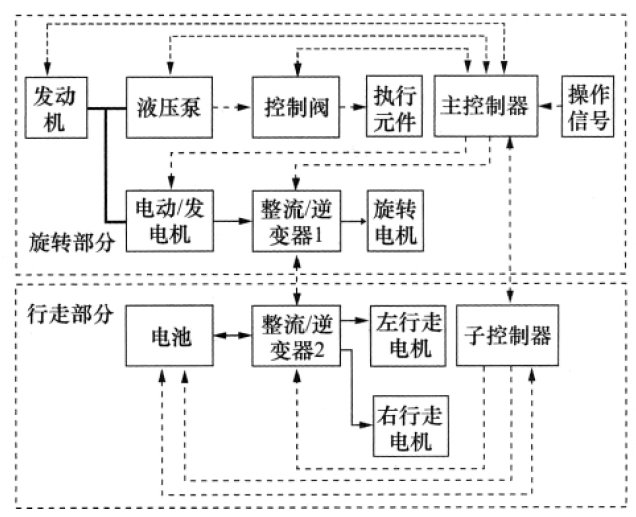
图16日立建机的混合动力液压挖掘机结构
图17为日本小松混合动力液压挖掘机系统,采用并联式混合动力系统,系统有一个单独的能量回收液压马达和发电机,使用电机驱动回转体能够减小发动机的功率,控制器根据操作信号和反馈信号来控制发动机、电池、整流器、逆变/整流器和控制阀。
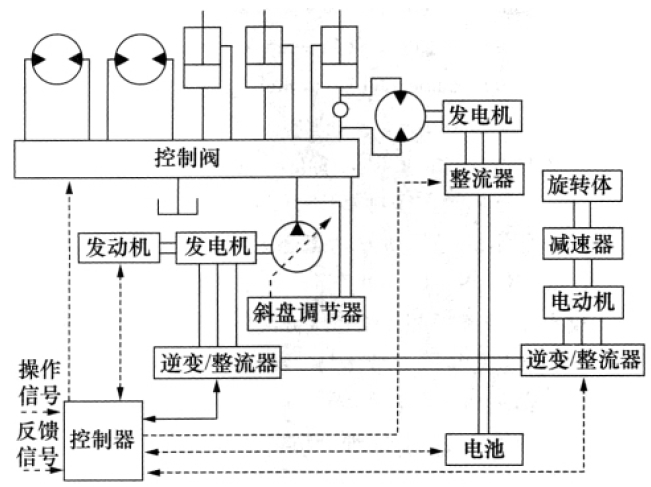
图17小松的混合动力液压挖掘机系统
图18为日本神户制钢所的混合动力挖掘机系统。与前面不同的是它采用串联式混合动力系统,发动机输出的机械能全部转换为电能,供给四个电动机驱动动臂、斗杆、铲斗油缸和左右行走以及回转马达。蓄能装置采用电池和电容的组合,分别利用了电池的高比能量和电容的高比功率。系统的势能、惯性能和制动能可以通过液压马达和电动/发电机回收,直接转换为电能后存储在电池和电容中。
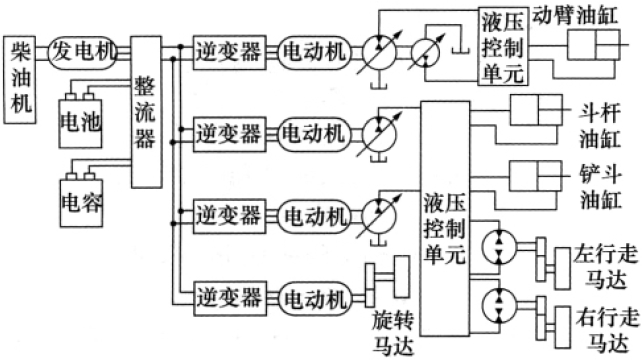
图18神户制钢所混合动力挖掘机系统
前面介绍了工程机械通过使用混合动力技术,在载荷波动时稳定发动机到低油耗工况工作实现恒功率输出,从而实现了节能减排方面的目的,除了混合动力技术以外还有一项技术也可以实现相同功能,那就是CVT(ContinuouslyVariableTransmission)静压无级传动技术。
图19为卡特彼勒近年来推出了966KXE中型轮式装载机,它采用了CVT静压无级传动技术。CVT将发动机传递来的动力分成两条路径传递出去,一路通过机械方式,另一路通过液压泵和液压马达变速传递。
由于该液压系统可以无级变速,因此整个变速箱具备连续可变速的特性。通过调整液压进行无级变速,使得发动机转速与机器速度无关,发动机可以长时间工作在高效区。由于取消了变矩器,也就没有了前面所说的液力变矩器效率损失。卡特声称966KXE燃油效率的提高最高可达25%,在集料工况下,连续CVT静压无极传动比传统装载机可节省一半的能量消耗。
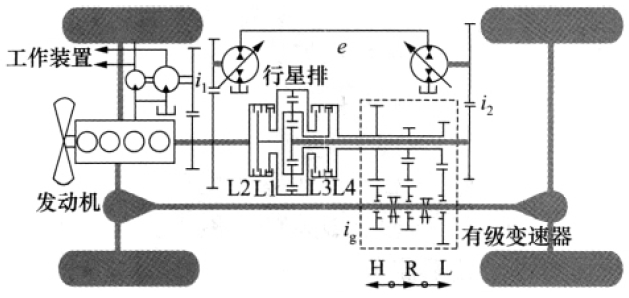
图19卡特彼勒966KXE混合动力装载机
从前面的介绍可以看出,为稳定发动机到低油耗工况,实现恒功率输出,所采用的混合动力技术与CVT静压无级传动技术所涉及的传动形式较多,包括机械传动、液压传动、液力传动、再加上电传动。甚至这四种传动形式同时用在同一种工程机械上的也有,如前面介绍过的沃尔沃L220FHybrid轮式装载机。用微电子技术同时管理好这四种传动,并且将发动机的输出稳定在低油耗区,是一项具有挑战性的工作。因为这需要多学科的综合才能完成,包括电控发动机技术、计算机与总线技术、微电子技术、电力电子驱动技术、液力传动技术、液压传动技术、机械动力学等等。
从实用的角度来看,一项新的技术应用在工程机械上,所增加的成本必须能够在机器的全生命使用周期内补偿回来,否则就不会对消费者产生太多的吸引力。科学的魅力在于“用简单的技术解决复杂的问题”,而不是越复杂越好。从本节介绍的多种节能技术来看,效果最好的还是复合在一起的传动形式相对比较少的传动系统,如川崎65ZHybrid装载机、约翰迪尔644KHybrid装载机、卡特彼勒966KXE装载机、小松PC200-8型挖掘机等。作者建议既使使用混合动力也不要设计过多的驱动形式,除机械传动外最多再使用两种为宜。这不仅仅是因为成本的问题,最主要的是易于实现各种传动技术的信息化综合,使发动机稳定在低油耗区工作。
5、结论
机械传动、流体传动与电传动是工程机械的主要传动形式,它们伴随着工程机械行业的发展虽然得到了不断的完善,但真正使工程机械传动性能产生质的飞跃还是在信息化技术的应用与普及之后。本研究分析了信息化对工程机械传动技术的影响,概括了工程机械传动技术信息化的4种发展趋势,即由流体、机械处理动力流信息逐渐走向由微电子技术处理动力流信息,由复杂的多路阀控制的流体动力系统逐渐走向由总线和分立电控元件控制的动力系统,电传动的应用逐步增多,动力源的输出向恒功率输出方向发展,这些为我们今后的科研工作提供了参考方向。
当前信息化技术仍然在高速地发展和不断地进
步,这为我们改进工程机械传动系统提供了无限的可能性,同时工程机械施工技术的发展也会对其传动系统提出更高的技术需求,促进信息化技术本身的发展及其在工程机械领域的集成与应用。可以说工程机械传动技术正迎来一个黄金的发展阶段,我们从事传动技术研究的科技工作者应该抓住这一难得的机遇,选择与把掘好自己的科研方向,不断开拓进取,为实现更高效、更智能、更节能、更环保的工程机械传动系统发展目标做出自己的贡献!