在现代各类精细化工品生产过程中,精馏装置往往在炼化企业内的能耗上占有很大的比重。据统计,一个炼化企业内,能量的40%消耗在精馏过程。目前,精馏装置为了保证产品合格,一般会采取保守的操作参数和操作方法,如此便会产生不合理因素,比较常见的便是分离过度。但受迫于迅速升高的能源价格,企业均将降低能耗作为生产过程中的重点控制工程,这也成为化工设计工作者所关注的重点。故对精馏塔的节能优化的研究探讨对石油化学工业生产有非凡的意义。
1、进料温度与位置
1.1进料温度
塔的模拟表明,精馏塔的分离动力来自塔釜重沸器的热量,而且全塔上下的负荷并不均匀,与侧线采出与进料工况有关。从气液量上讲,塔底相较于塔顶往往是大的,所以一般塔的液泛从塔底开始进行。当选择冷态进料时,就要求塔釜重沸器更多的热量供应,同时增加塔底气液量。保持已知的分离状态下所需要的热量不变,当精馏系统的进料温度逐步升高,重沸器的热负荷相应减少。
1.2进料位置
进料位置的选择上,就需要提到最佳进料位置。最佳进料位置是指在相同的理论板数和同样的操作条件下,具有最大分离能力的进料板位置或在同一操作条件下所需理论板数最少的进料板位置。最佳进料口位置的选择原则是应该保持此进料口位置与该精馏塔相应位置的温度接近。在进料位置比最佳进料位置高的情况下,则当前状态下进料板液相组成中的小质量组分会比最佳进料位置下此板的液相组成的小质量组分要高,同时大质量组分相应会比最佳位置下的液相组成要低,在这种情况下,相比于最佳位置,相当于减少了精馏断的塔板数,增加了提留段的塔板数,故此时塔顶产品质量会明显下降,塔釜大质量组分的质量会提高。同理,在进料位置比最佳进料位置低时,则当前状态下的进料板液相组成的小质量组分会比最佳位置下该板的液相组成的小质量组分要低,同时大质量组分相应会比最佳位置下液相组成要高,相比于最佳位置而言,相当于增加了精馏段的塔板数,减少了提留段的塔板数,故此时塔顶产品质量会明显提高,塔釜大质量组分的质量会下降。
一般情况下,确定精馏塔进料位置主要根据物料组成,所选择的进料位置应当使在该塔板的组成与进料组成相近,否则容易引起返混现象,进而降低塔板效率。
2、最佳回流比
在以往的工程设计项目中,工程人员处于保守原则往往将塔设计得相对较小,这样就带来一个问题,需要取一个较高的回流比值。这种做法在实际操作上并不会对生产需要造成影响,反而能提高产品纯度,亦为以后提高塔的操作负荷留下空间。从而能明显看出,若要维持塔的正常运转,必须提高回流比,另一方面则会流失浪费大量能量,回流比R 与整体费用的关系详见图1。
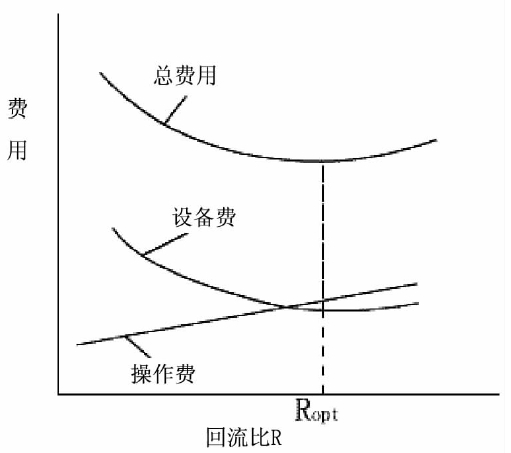
图1 回流比R与费用的关系
2. 1 回流比R与操作费用
操作费用主要指精馏过程的能量消耗。在精馏塔系统中,消耗的能量分为两部分,一部分是指精馏塔底部重沸器的热负荷QB,另一部分则是精馏塔顶部冷却器的热负荷QC,以上两者均随着塔内上升蒸汽量的增大而不断增大。而精馏塔内的蒸汽增量随着R 的升高而减小,关系式如下:

在工艺条件一定的情况下,q、D、F 均为定值,那我们可将( 1) 、( 2) 两式简化如下:

式中:
D———塔顶精馏出的液量,kmol /h;
q———进料状态参数;
RD———塔顶蒸汽的平均冷凝热量,kJ /kmol;
Ig———重沸器内上升蒸汽的焓( 摩尔) ;
IW———塔底产品的焓( 摩尔) ;
Q———重沸器的热量损失,kJ。
由以上可知,在精馏过程中所产生的能量消耗与R 值是成正比。所以,回流比R 对精馏过程中的能量消耗有重大的影响,如能降低回流比,降显著降低能量消耗,减少操作费用。
2.2回流比与设备费用
回流比越小,对应需要设置的塔板数量就会越大,显然设备塔板数量不能过大,否则设备的费用将会占据过大的投资额而显得不经济; 回流比越大,设备费用明显降低,但当超过某一临界值后,也将增大塔底重沸器与塔顶冷凝器的工作负荷,综合设备费用反而是增加的。
2.3回流比取值发展趋势
近些年我过化工领域的飞速发展,化学物质的物性数据、计算算法的完善,加上日益提高的自控水平,回流比取值呈现下降趋势。目前该值由过去的传统的在( 1. 3 ~ 2. 0) Rmin 之间取值慢慢向( 1. 1 ~ 1. 3) Rmin 之间取值,取值日益向最小回流比靠。
3、精馏塔内件选择
顾名思义,精馏塔是一种精馏装置。一般精馏塔均采用塔式汽液接触方式设计,并且分为填料塔与板式塔。
3.1板式塔内件选择
板式塔用于气体与液体、液体与液体之间系统的分级接触传质设备,一般由塔体和塔板组成。塔板根据一定间距水平装置在塔内。由于其为板式塔中进行传质的关键部位,所以塔板是影响板式塔能量消耗的重要部件。
在一般设计上,塔板会被均匀地开有一定数量通道,这些通道为气体从下至上穿过板上液层提供路径,以此来保证不同相态介质进行充分接触。气体通道有许多不同形式,它决定着塔的性能,我们也以此区分塔的类型。
在评价塔板的性能方面,存在五个指标: 产能大,效率高,压降小,操作弹性大,结构简单。不过在实际工程设计中,任何一种塔板都不可能完全满足上述的所有指标要求,它们往往各具特点,这就需要我们根据不同工艺流程、工艺参数和工艺目的进行选择。
3.2填料塔内件选择
填料塔是化工企业中常见的气液传质量设备之一,塔内填料至一定高度,用以扩大流体间的接触面,由于其结构简单,日后的生产过程中便于检修,所以在吸收、精馏、解吸等操作领域均有广泛的应用。
作为填料塔的核心部件,填料方面又有不同的做法,一般比较常见的可分为散堆填料和规整填料。散堆填料由颗粒体组成,其颗粒体具有不同的形状尺寸,散堆于塔内。规整填料具有相同的、成块的、规整的结构。由于其排布均匀、堆砌规整,为气液规定走向,可以很大地提高精馏塔整体性能。
填料塔内一般都会安装分布器,此举旨在充分发挥填料的效率,原理是使填料层顶部的液体分布更加均匀,减少液体不良分布所带来的放大效应,提高传质传热的有效接触面,进一步而提高塔的效率。
4、总结
综上所述,从多方面角度我们依然可以找到降低精馏系统能耗的途径,并有一定程度的节能作用,但经济效益决定了对其的最终评价。往往操作费用会随着节能技术的采用而降低,但同时节能设备的增加则使得设备投资增加。从经济学上讲,最大限度地节能并不能满足经济性要求,而且节能措施往往涉及更为复杂、苛刻、要求较高的控制水平。所以在进行决策时需要权衡节能成本与经济效益之间的关系,采用最合适的方案。