含油污水处理技术的发展是油田环境保护工程的重点。对于高浓度的含油污水,用沉淀法就可以分离,但是对于低浓度(≤500 mg/L)的含油污水,沉淀法难以取得良好的净化效果。气浮法作为一种快速、高效的固液分离技术,除油效果更好,既能代替水处理上的沉淀、澄清过程,又可作为含油污水深度处理的预处理之用。
随着对浮选过程和机理研究的深入,发现已有的气浮实验装置存在的不足主要在于:设备庞大、费用高、整体工艺复杂、微气泡大小不均匀、除油效率不稳定。因而设计简单易行、处理效果优良的浮选装置就成为研究的中心问题。
1、气浮除油方法
油田开采后期,采出液中的含水率在不断上升,因而产生的含油污水量也在不断增大,如何降低污水的处理费用,提高处理后的水质标准,受到人们的广泛重视。采用气浮除油技术可使污水在罐内的停留时间大大缩短,除油效率提高,减少污水的处理费用和基建费用,提高处理后的水质指标。
1.1 气浮分类
根据微细气泡产生方法的差异,气浮除油技术包括溶气气浮法、分散空气法和电解法。
应用较多的加压溶气气浮法能耗大,对操作条件要求高,而电解气浮法不适用于大规模水处理。因此需要开发一种操作简单,而分离效率高的气浮装置以适应油田开采后期含油污水的处理过程。
1.2 发泡方式
对于不同的发泡方式,由于发泡机理不同,产生的气泡尺寸大小及其影响因素也不尽相同。前人研究表明,气泡尺寸大小会影响气泡携带固体颗粒的能力、浮选的选择性、处理能力等。因此,选择合适的发泡方式相当重要。
常用的气泡发生方式有:1)剪切接触发泡:高速流动的矿浆和气体以适当方式接触,如通过金属网或充填介质产生气泡;2)机械搅拌发泡:通过叶轮高速旋转造成负压吸入空气,并通过湍流边界层的大小和方向都瞬时变化的剪切力将气流粉碎形成气泡;3)射流发泡:受压气流喷入矿浆或者矿浆喷入气流均可产生适合浮选的气泡;4)降压或升温发泡:空气在水中的溶解度大约为2%,当升高温度或者降低压力时,溶解的气体析出产生气泡;5)微孔发泡:气体通过微孔塑料、橡胶、帆布、尼龙、微孔陶瓷管甚至卵石层发泡;6) 电解水产生气泡;7)超声波发泡。
2、气浮除油装置设计
气泡和油滴间的相互作用是影响气浮效率的关键。因此,针对气泡和油滴的碰撞、粘附过程,为了进一步提高气浮效率,需增加气泡数量加大碰撞机率;加入表面活性剂增加粘附效率;设计布气均匀的微气泡成泡板,使气浮器内流场稳定。
2.1 气浮装置基本结构
整个实验装置由气浮柱和供气系统两大部分组成。气浮柱总高1.63 m,内径120 mm,由3 部分组成,自下而上依次为集气室、微气泡成泡板、气浮筒。
其中气浮筒高1.6 m,用于气浮分离。3 个水嘴分布于一侧,分别位于气浮筒的上、中、下3 个位置,根据实验时液位高度的不同,可以充当出油口和出水口,起到排污、排水及取样的作用。气浮柱的主要材料为有机玻璃,将其设计成高径比较大的立式圆柱形结构不仅可以使气泡与含油污水均匀分布,还可以承受较高的水力负荷。
供气系统主要由氮气瓶、减压阀、玻璃转子流量计组成。相较于传统气浮装置占地面积大、运行效率低且费用高等缺点,该气浮装置突出了占地面积小、装卸简便、运行效率高和投资小等优点。
2.2 微气泡成泡板
微气泡成泡板位于集气室和气浮筒的连接处,可拆换,是产生气泡的关键装置,其材料、结构、排布形式决定了气泡的大小、数量和在浮选器中的分布,而这些因素又是决定气浮效率的关键。
选用半径为60 mm 的不锈钢圆形金属盘片,金属盘片的厚度在能打微孔的前提下尽可能厚。采用激光打微孔的方式,共加工3 个半径为60 mm 的带微孔的金属盘片,微孔的直径分别为20、30、50 μm,分别标记为1# 盘、2# 盘、3# 盘,以便于使用时区分。为保证布气均匀,每个盘片从圆心开始,分别在半径5、10、15、20、25、30、35、40、45 mm 的圆上,以大约5mm 的弧长间距均匀钻微孔(见表1)。

表1 微气泡成泡板微孔分布
2.3 气浮流程
氮气瓶内的氮气压力高达5 MPa,经减压阀减压后,沿导气管流经玻璃转子流量计,从气浮柱底部通入,气体先聚集在集气室,使集气室内的压力逐渐升高,直至有足够的压力使气体可以通过微气泡成泡板的微孔。气泡在微气泡成泡板处产生后就进入了气浮筒,气浮筒是进行气浮分离的场所,所以又叫气浮分离室。通气后将事先已混合均匀的定量待处理水与定量浮选剂从浮选柱顶部缓缓倒入,倒完后,微气泡均匀分布在气浮筒内并在浮力的作用下向上运动,微气泡在向上浮升的同时携带着水中的悬浮颗粒物或油滴上升到液面,形成浮渣层,随着气浮的进行浮渣层的厚度不断增加,可将其从上方的出油口排出。实验过程中,可以根据液位的高低灵活选择中间或下方的出水口进行取样,气浮结束后,污水从气浮柱底部排出。
3、气浮除油实验
选取某油田的含油污水,含油浓度为245.6mg/L,在室温、处理水量2 L、液位高度250 mm 的条件下,研究气浮时间、加剂量、进气流量及微孔孔径对气浮装置除油效率的作用规律。
3.1 气浮时间
通过研究除油效率随气浮时间的变化规律,从而确定气浮柱的稳定时间。所用的清水剂为0.2 g,微气泡成泡板为3# 盘,进气流量为1.0 L/min。
气浮一共持续了30 min,在20 min 以内,除油效率随时间的增长而提高,并且除油效率的增长率随时间的增长而逐渐趋缓,过了20 min 后,整个气浮装置的除油率随时间的延长而基本保持不变(见表2),说明此时系统已经达到一个稳定的状态,通过延长气浮时间来增加除油效率的方式已经不适用了。
因此,本着节能、高效的原则,选择最佳气浮时间20 min 作为之后每个实验工况的气浮时间。
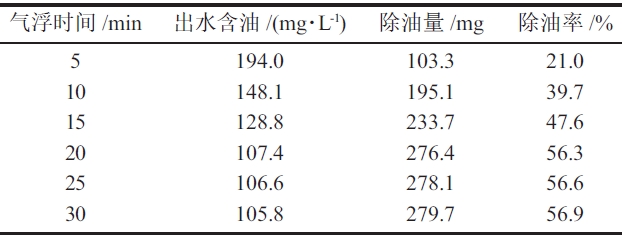
表2 气浮时间对除油效率的影响
3.2 加剂量
考察清水剂剂量对除油效率的影响,选择的进气流量为1.0 L/min,气浮时间为20 min。
虽然3 块微气泡成泡板的微孔孔径不同,但是各自的除油效率对于加剂量的变化趋势是一致的(见表3)。很明显,随着清水剂剂量的增加,除油效率逐渐提高。当剂量增加到一定量时,气浮效率基本不再变化,而是稳定在一个最高值。可以看到,加剂量在1.0 g 以后,除油效率趋于稳定。
因此,在该实验条件下最佳剂量是1.0 g,即最佳浮选剂浓度为500 mg/L。
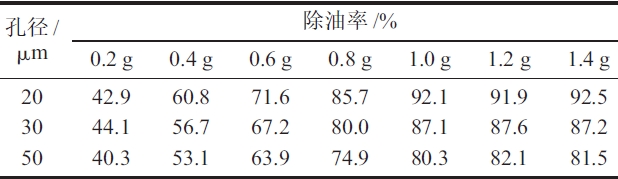
表3 不同加剂量下的除油效率
3.3 进气流量
在最佳气浮时间、最佳剂量已经确定的情况下,进一步研究除油效率随进气流量的变化规律,从而确定该气浮系统的最佳进气流量。
实验前,先给气浮柱注入2 L 自来水,观察气泡的形态随进气流量的变化,以确定实验流量点分布。
观察发现,当进气流量达到0.6 L/min 时,气浮筒内开始出现气泡,但气泡产生形式大多是先在微气泡成泡板表面生成,慢慢长大,再脱离板面向上浮升,能用肉眼观察到的连续气泡群很少。随着进气流量的增大,气泡群的运动由间断逐渐变为连续,气泡均匀连续地从微孔中冒出,并沿直线上升,上升过程中气泡大小不变。当进气流量超过2.0 L/min 后,气泡群的运动轨迹由直线逐渐变成S 形,即气浮筒内气泡运动呈紊流,杂乱无章。因此,本实验选取4 个进气流量实验点为0.6、1.0、1.5、2.0 L/min。所用清水剂剂量为1.0g,气浮时间为20 min。
除油效率随进气流量的增大,呈先增加后减小的趋势,当进气流量达到1.5 L/min 时,除油效率达到最高值(见表4)。
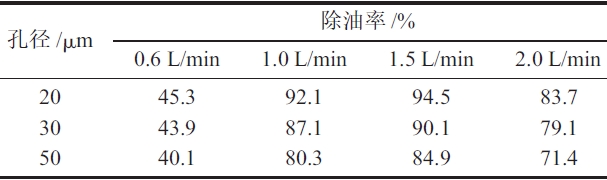
表4 不同进气流量下的除油效率
初期进气流量小,成泡板产生的气泡数量少且不连续,导致气泡与油滴或固体悬浮颗粒碰撞粘附的概率很小,除油效率低。随着进气流量的增大,气泡数量迅速增加且呈平推流,气泡与油滴或固体悬浮颗粒碰撞粘附的概率大,除油效率显著提高。但当进气流量增加到一定值时,过大的进气流量使得气泡数量过多而出现气泡间相互兼并的现象,反而减少了粘附油滴或固体悬浮颗粒所需的小尺寸气泡数量,并且气泡运动呈紊流,对浮选柱内流体环境产生剧烈的扰动,最终导致除油效率降低。
因此,可以得出结论:气泡运动呈平推流是气浮处理含油污水的最佳状态,利于提高除油效率。即进气流量应控制在一个最佳范围,本实验的最佳进气流量是1.5 L/min。
3.4 微孔孔径
从表4 中不难发现,3 块微气泡成泡板的除油效率随孔径变大而降低。而孔径的大小及分布直接影响到气泡的大小及分布,也就是说至少在微气泡成泡板孔径范围为20~50 μm 内,产生的微细气泡越小,除油效率越高。
同时,还可以找出除油效率最高的点,发现其对应的实验参数为清水剂500 mg/L,气浮时间20min,进气流量1.5 L/min,成泡板孔径20 μm。在最佳实验参数下进行气浮的除油效果,经气浮后可以明显看到,污水中的油大量漂浮于液面或粘附在气浮筒壁上,污水也从浑浊变为清澈。
孔径对微细气泡的影响主要体现在两个方面:
1)影响气泡大小。在微气泡成泡板处产生微细气泡有两个步骤,先是气泡在微孔处膨胀,再是达到一定体积后脱离板面而浮升。微孔的直径直接影响通过微孔的表观气速,孔径越小,表观气速越大,对正处于膨胀阶段的微细气泡的作用力也就越大,致使气泡在脱离板面时体积相对较小,即产生携带油滴或固体悬浮颗粒所需的小气泡。
2)影响气泡产生速率,即气泡数量。表面上看气泡数量似乎只和进气流量有关,其实孔径也是一个不可忽视的因素。小直径的微孔提高了表观气速,使气泡迅速脱离成泡板面,加大了微细气泡的产生速率,即单位时间内产生的气泡数量大大增加。与此同时,足够大的初速度可以保证气泡碰撞粘附油滴或固体悬浮颗粒后,气泡和油滴或固体悬浮颗粒之间还有一定的动能用来顺利排出水膜,使油滴牢固地附着在气泡上。
4、结论与建议
针对油田后期采出水的特点,在室内小型气浮实验装置基础上,以某油田的含油污水作为处理水样,通过间歇操作的方式系统研究了气浮时间、加剂量、进气流量、微孔孔径等各种因素对除油效率的影响,得出以下结论:
1)除油效率随时间的增加而增加,但气浮时间超过20 min 后,除油效率基本保持不变;
2)实验确定清水剂的最佳浓度为500 mg/L;
3) 液位高度一定,随着进气流量的增大,除油效率先增大后减小。实验确定在最佳剂量下的最佳进气流量为1.5L/min;
4) 微气泡成泡板的孔径越小,除油效率越高。在实验的3 块不锈钢成泡板中,微孔直径为20μm 的1# 成泡板除油效率最高。
可见,在最佳实验参数下,该气浮装置的除油效率高达90%以上,为后续开发和设计连续式气浮装置提供基础数据和指导。